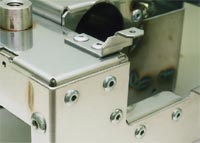 |
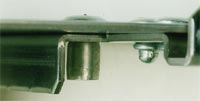 |
写真2〜3 リベット構造を採用し、大幅に納期短縮 |
|
こ |
の製品は、眼鏡フレームにあわせて眼鏡レンズの外周を研磨する機械のフレーム。従来、鋳物フレーム体でしかつくれなかったものを、精度と強度を確保しながら、板金組立方式で構築したノウハウが、高い評価を受けた。
「精度と剛性の確保には苦労しましたが、マシニング機械加工が不要になる分、リードタイムの削減と大幅なコストダウン、さらには在庫のゼロ化を実現することができた。お客様のニーズにどのように応えていくか、提案型企業としてのわが社の取り組みが、このような形で評価されたのは大きな喜びですし、そうしたチャンスの場を与えてもらったこともあわせて感謝しています」(大林根生社長)
材質はSUS430CP、板厚は2.0mm、要求精度は±0.2mm(一部±0.05mm)、1ロット50個、加工時間は1個210分。
|
|
板 |
金化にあたっての一番のポイントは、求められる精度・リードタイム・コスト面のすべてをクリアするために、溶接加工をほとんど不要にした、リベット構造の採用にある。
リベット構造の利点は、リベット用穴あけの段階で精度だしができること。穴位置がそのまま精度となるために、位置ずれや歪みが出にくく、また熟練技術者も必要とせず、加工時間も大幅に短縮できたのである(リベット接合箇所は52カ所)。ちなみにこのリベット構造は、特殊なボルトを差し込み、引き上げるだけ。ボルトを引っ張り上げることによって裏側部分の外形が膨張し、完全に密着する仕組みで、裏に手が回らない箇所も簡単に接合できるという大きなメリットがある。
次にリベット構造だけでは不足がちな剛性を補うために、約30カ所の点付け溶接を行っている。このTIG溶接による点付けは、溶接棒を使わず材料と材料を溶かして溶接しているので、溶接による位置ずれや歪みも発生しない。
点付けの中でも最も高い技術が要求されるのが(同社のノウハウでもあるのだが)、眼鏡レンズの外周を研磨する際に基準となる2点間(図中のA・Bの箇所)の精度出しである。この部分はこの製品の心臓部でもあり、100分台の精度(±0.05mm)が要求されるからである。このため、この箇所だけは高精度に加工された装着冶具を使用しながら点付け溶接するという、非常に高度な加工法が駆使されている。
この結果、従来60日のリードタイムを15日に短縮、また約3分の1のコストダウンを実現。現在まで約2000台を出荷している。
「設計にあたって私が最も配慮したのは、熟練技術者を必要としない、誰でもが加工、組立ができる加工法でした。リードタイムの短縮もコストダウンも、すべてがそこに集約されていく、という思いがあるからです。その考え方はこの製品に限らず、わが社が提案する加工法のすべてに精通しています。
リベット構造は、この製品で採用する以前から導入している加工法ですが、現在では、わが社の筐体加工の80〜90%はこの方式で行われています」(この製品の加工法を開発した奈良小太郎常務取締役)
|
|
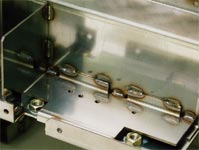 |
写真4 剛性を補うため30カ所の点付け溶接を行っている。
図1 受賞製品の構造図(下) |
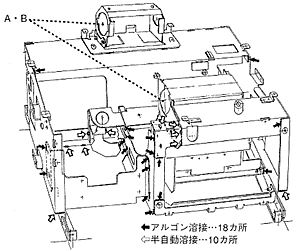
|
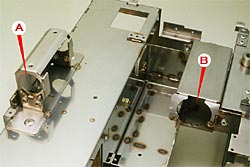 |
写真6 AB間は(図1のA・B部)は100分台の精度が要求される。 |
|
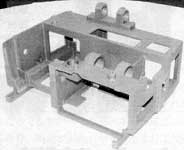 |
写真5 以前は鋳物構造で作られていた。 |
|
社 |
長室の四方の壁は、提案型企業としてお客様の厳しいニーズをクリアしてきた勲章ともいえる、お客様からの感謝状が所狭しと飾られているが、いま新たな取り組みとして社内ネットワークの整備が進行中である。3D/2D-CADデータの取り込みに対応したCAD/CAMシステムおよび生産管理・工程管理システムの導入、またインターネットを介しての製品データの取り込みなど、“IT板金工場”を目指して各種施策を推し進めている。
「お客様のニーズが厳しければ厳しいほど、わが社の出番だな、という思いは強い。これからもダイナミックなコストダウンにつながる提案を目指していきたいと思っています」(大林社長)
|
|
■多摩電子株式会社
本 社 神奈川県相模原市橋本台3-2-26
TEL042-773-7761
創 業 昭和41年
設 立 昭和44年
代表者 大林 根生
資本金 1300万円
社員数 70名
事業内容 電子機器構造設計、電子計算機筐体、
金融機器筐体、自動改札機筐体、発電制御中央電子
盤筐体、その他、通信・情報・電子機器の精密板金、
プレス部品加工一式。 |
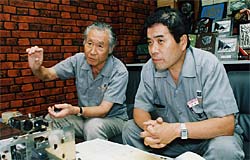
大林根生社長(左)と開発設計担当の奈良小太郎常務 |