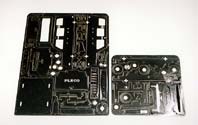 |
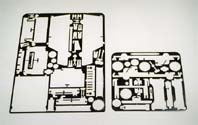 |
写真2〜3 自動車を組み立てるためのパーツ。レーザー加工機のみでカッティングし、62点が組み込まれている。 |
|
こ |
のプラモデルは、端材の鋼板(SUS304)に組立部品を組み込み、それを外して組み上げたもの。曲げ・溶接を一切用いず、レーザー加工機だけでこれだけ複雑な製品をつくりあげた造形力と、きちんと組み上げていくために不可欠な高精度(要求精度±0.1mm)の切断技術が評価された。
この製品をつくる契機となったのは会社案内をつくるときに、“会社の加工技術をアピールする、造形的なイメージ製品を掲載したい”という要望があったため。このときの製品が写真10の飛行機。発想は「知恵の輪みたいに、組む順番を間違えたら組み上がらないものをつくったら面白いだろう」(小林真一社長。以下同じ)という気軽な気持ちだった。
しかし、新入社員にやらせてみたところ、意外と簡単に組み立てる。次に小林社長は、組立手順を難解にするために組立部品数を増やし、また2種類の板厚(飛行機は1.5mm、自動車は1.5mmと2.0mmの2枚)を用いて取り組んだのが自動車である。これが、お客様を含め関係者の間で評判になる。あまりにも組立順序が複雑なために、誰もが挑戦心をかき立てられるからであった。
「レーザー加工機による高精度な切断技術をアピールするため。見本としてお客様に渡していました。組立順序も含めて難度の高い加工という自負があります」
|
|
最 |
初は自動車の絵を描き、組立順序を想定して、組立部品をどのようにバラしていくかを設定しながらCADでプログラムをしていった。そこにはいくつかのアイディアと工夫が盛り込まれている。
@ 切断時間を短縮するために、板厚の違う2枚のステンレス板に展開されたパーツは全て“一筆書き”になっている(加工時間約17分)。
A ミクロジョイント部分は、組立中に手を傷つけないために、組立部品の内側に切り込まれている。
B 62点のパーツからなる。ちなみに組立はシャーシから始まり、屋根部分で終わる。
C ハンドル位置(左か右か)を間違えると、フロント前面の文字が逆さ文字になる。その場合は全部バラして、もう一度、一から組み直さなければならない。
|
|
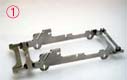 |
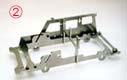 |
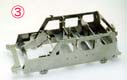 |
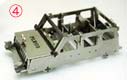 |
写真4〜7 @からCの順序で組み立てられていく。最後に屋根部分を組み込んで写真1の完成品となる。 |
|
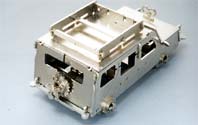 |
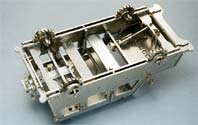 |
写真8〜9 後方部と、下部から見た状態。車輪も回転する。 |
|
フ |
ェアの銀賞受賞は、今回で2度目。小林社長は次のように話を総括してくれた。
「これだけ高精度な加工技術が可能な会社の総合力を見て欲しいですね。実務においては、受賞製品以上の心配り、創造力、技術力を駆使して日々製品加工に取り組んでいるということです。試作そして製品加工は図面通りにつくるだけでなく、いまつくっている部品は、製品のどの部分に位置するかなど、自分で考えながら物作りをすることが大事なのです。創造力を育む習慣をつけていかないと、本当にいいものはできません。そして今回の加工はすべて現場にまかせましたが、確実に若い人が伸びてきているという確証を得たことも大きな収穫となりました」
いま、自動車に代わる新しい製品を待望する声が大きいという。次回のフェアには、より高度で難解な新しい製品を見たいものである。
|
|
■プレコ技研工業株式会社
本 社 広島県福山市箕島町6280-15
福山テクノ工業団地内
TEL 084-920-3320
設 立 1970(昭和45)年6月
代表者 小林 真一
資本金 3800万円
社員数 23名
事業内容 精密板金・精密機械・精密プレス加工
および金型設計製作など
U R L http://www.pleco.co.jp
E-Mail 会社宛の事務連絡等 pleco@pleco.co.jp
CADデータ data@pleco.co.jp
社長宛直通メール kobayashi@pleco.co.jp |
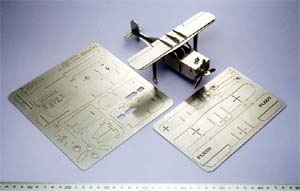 |
写真10 プラモデルの1号製品となった飛行機 |
|